Deciphering the Enigma of Porosity in Welding: Tips for Reducing Problems and Optimizing Quality
In the detailed world of welding, porosity remains a persistent obstacle that can substantially influence the top quality and integrity of welded joints. As we delve right into the midsts of porosity in welding, uncovering the secrets to its avoidance and control will certainly be critical for specialists looking for to master the art of premium weldments.
Understanding Porosity in Welding
Porosity in welding, a common concern encountered by welders, refers to the presence of gas pockets or gaps in the bonded product, which can compromise the stability and high quality of the weld. These gas pockets are normally trapped throughout the welding procedure due to different aspects such as inappropriate securing gas, polluted base products, or incorrect welding criteria. The development of porosity can compromise the weld, making it susceptible to fracturing and deterioration, eventually leading to architectural failings.
Recognizing the origin of porosity is essential for welders to properly prevent its event. By recognizing the significance of keeping proper gas protecting, making sure the cleanliness of base products, and maximizing welding settings, welders can substantially reduce the chance of porosity development. Furthermore, using methods like preheating the base product, using proper welding techniques, and carrying out detailed assessments post-welding can additionally aid in reducing porosity issues. On the whole, a detailed understanding of porosity in welding is crucial for welders to generate top quality and resilient welds.
Typical Reasons of Porosity
When inspecting welding processes for potential top quality issues, understanding the usual reasons of porosity is necessary for maintaining weld honesty and preventing structural failings. Porosity, defined by the existence of cavities or spaces in the weld steel, can dramatically endanger the mechanical homes of a bonded joint.
Additionally, welding at improper parameters, such as exceedingly high traveling rates or currents, can generate extreme disturbance in the weld pool, capturing gases and triggering porosity. By resolving these common reasons through appropriate gas protecting, material prep work, and adherence to optimum welding specifications, welders can minimize porosity and boost the top quality of their welds.
Methods for Porosity Avoidance
Executing effective safety nets is critical in lessening the occurrence of porosity in welding procedures. One strategy for porosity avoidance is making sure proper cleaning of the base steel prior to welding. Impurities such as oil, oil, rust, and paint can bring about porosity, so thorough cleansing making use of appropriate solvents or mechanical approaches is essential.

An additional secret safety net is the option of the appropriate welding consumables. Utilizing high-quality filler materials and securing gases that appropriate for the base metal and welding procedure can significantly minimize the risk of porosity. Additionally, maintaining appropriate welding criteria, such as voltage, current, travel rate, and gas flow rate, is important for porosity prevention. Differing the suggested settings can result in improper gas insurance coverage and inadequate combination, causing porosity.
In addition, using proper welding methods, such as maintaining a consistent travel speed, electrode angle, and arc length, can aid protect against porosity (What is Porosity). Sufficient training of welders to ensure they comply with best practices and quality control procedures is also important in reducing porosity issues in welding
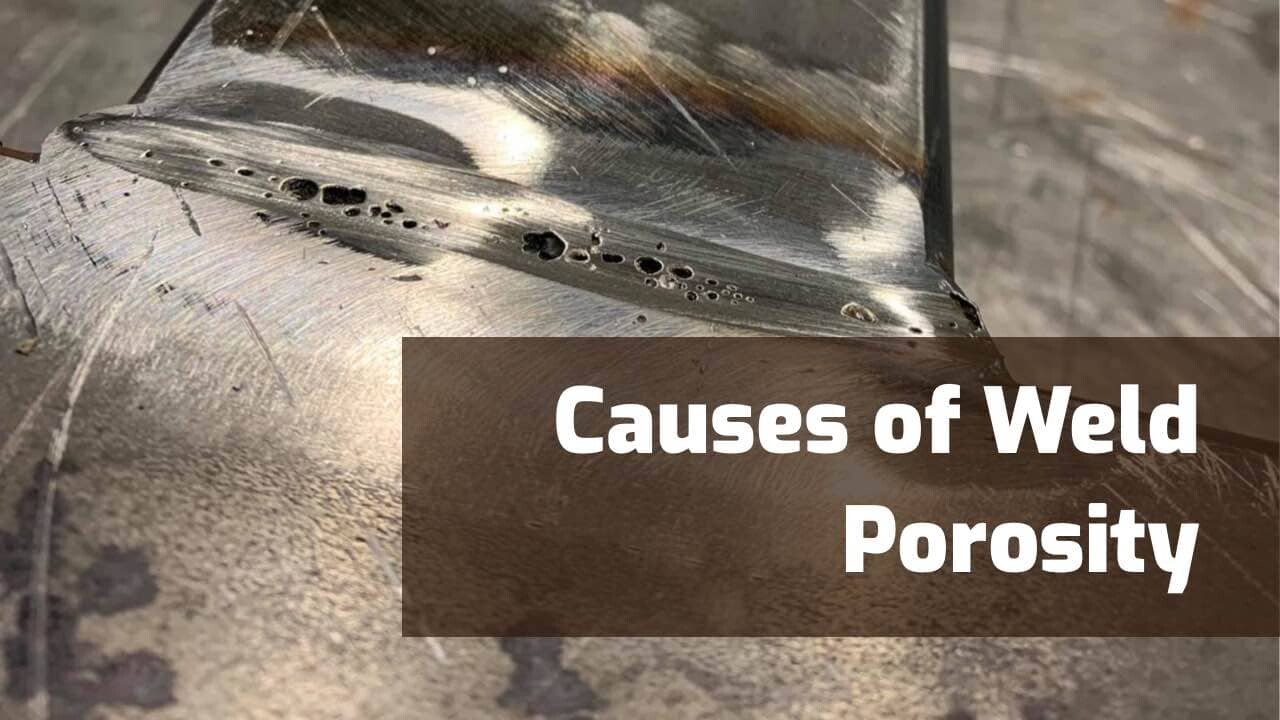
Finest Practices for High Quality Welds
One secret method is keeping appropriate cleanliness in the welding area. Extensively cleaning the workpiece and bordering area prior to welding can aid mitigate these concerns.
One more best practice is to meticulously select the proper welding criteria for the more certain products being joined. This consists of establishing the proper voltage, existing, travel rate, and securing gas flow my explanation rate. Appropriate parameter option guarantees optimum weld infiltration, fusion, and overall top quality. In addition, using high-quality welding consumables, such as electrodes and filler steels, can considerably influence the final weld high quality. Buying premium consumables can lead to stronger, much more sturdy welds with less defects. By complying with these best practices, welders can regularly generate high-grade welds that fulfill industry requirements and go beyond client expectations.
Value of Porosity Control
Porosity control plays a critical role in making sure the stability and quality of welding joints. Porosity, characterized by the visibility of tooth cavities or voids within the weld steel, can dramatically jeopardize the mechanical properties and architectural stability of the weld. Too much porosity damages the weld, making it extra at risk to splitting, corrosion, and total failure under operational lots.
Effective porosity control is essential for maintaining the wanted mechanical residential or commercial properties, such as strength, ductility, and sturdiness, of the welded joint. What is Porosity. By decreasing porosity, welders can improve the total top quality and integrity of the weld, guaranteeing that it fulfills the performance needs of the intended application
Moreover, porosity control is vital for achieving the desired aesthetic appearance of the weld. Too much porosity not only weakens the weld but additionally takes away from its visual appeal, which can be important in sectors where aesthetics are vital. Proper porosity control techniques, such as utilizing the proper shielding gas, managing the welding parameters, and making sure appropriate cleanliness of the base materials, are crucial for creating top quality welds with very little issues.

Conclusion
In final thought, porosity in welding is a common defect that can jeopardize the top quality of why not look here the weld. It is essential to regulate porosity in welding to make certain the honesty and stamina of the final product.
Comments on “What is Porosity in Welding: Ideal Practices for Avoiding Porous Welds”